|
ACCESS THE FULL ARTICLE
No SPIE Account? Create one
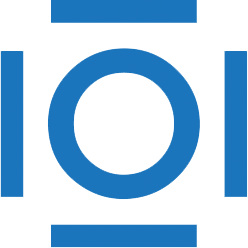
CITATIONS
Cited by 10 scholarly publications.
Aerospace engineering
Video
Velocity measurements
Data acquisition
Damage detection
Doppler effect
Optical testing