|
ACCESS THE FULL ARTICLE
No SPIE Account? Create one
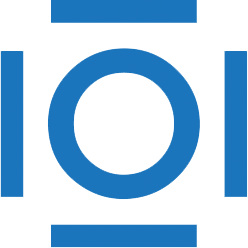
CITATIONS
Cited by 19 scholarly publications.
Sensors
Magnetic sensors
Remote sensing
Magnetism
Bridges
Temperature metrology
Calibration