|
ACCESS THE FULL ARTICLE
No SPIE Account? Create one
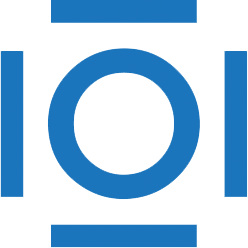
CITATIONS
Cited by 2 scholarly publications.
Shape memory alloys
Nickel
Palladium
Actuators
Binary data
Temperature metrology
Aerospace engineering