|
ACCESS THE FULL ARTICLE
No SPIE Account? Create one
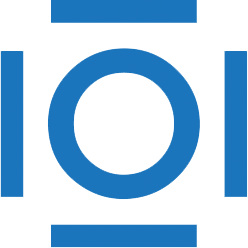
CITATIONS
Cited by 1 scholarly publication.
Surface finishing
Laser induced damage
Surface roughness
Polishing
Ellipsometry
Atomic force microscopy
High power lasers