|
ACCESS THE FULL ARTICLE
No SPIE Account? Create one
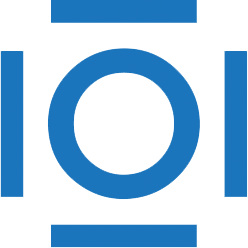
CITATIONS
Cited by 5 scholarly publications.
Microelectromechanical systems
Actuators
Chromium
Finite element methods
Data modeling
Sensors
Silicon