The telescope’s mirrors M1, M2 as well as the focal plane detector are supported by a thermally controlled CFRP structure suspended on isostatic mounts. The dimensional stability of the structural system supporting the optics is a key requirement as it directly impacts the instrument’s accuracy. The M1 and M2 mirrors are supported by a tubular CFRP telescope design which has been optimized by analyses down to carbon fibre layer level with the support of extensive sample test results for model correlation and accurate dimensional stability predictions. This sample characterization test campaign has been conducted on samples with different carbon fibre layups (orientation and stack sequence) to measure accurately the Coefficient of Thermal Expansion (CTE) over a wide temperature range extending from -80°C to +80°C. Using the correlated Finite Element Model, the fibre orientation layup that minimized the relative displacement between the M1 and M2 mirrors, including the consideration of the thermo-elastic contributions of the isostatic mounts on the overall stability of this optical system, has been identified and selected for the baseline design of the CHEOPS Structure. A dedicated Structural and Thermal Model (STM2), which was then refurbished to a PFM, was manufactured and tested with an ad hoc setup to verify the overall structural stability of the optical train assembly [2]. The relative distance between M1 and M2 was measured under thermal vacuum conditions using laser interferometer techniques. Thermal cycling tests were initially conducted to eliminate and characterize settling effects. Then, the structure’s stability was measured at three stabilised operational temperatures: -5, -10 and -15°C. The thermally induced M1-M2 misalignment on the optical axis was measured to be between -0.156 and -0.168 micron/°C. Relative mirror tilt and lateral centre shifts were also measured. The obtained focal distance, tilt and centre shift stability between mirrors M1 and M2 were all compliant with the system level requirements such that both an STM and PFM model of the CHEOPS CFRP Structure were successfully qualified and delivered in due time for integration on the spacecraft. |
ACCESS THE FULL ARTICLE
No SPIE Account? Create one
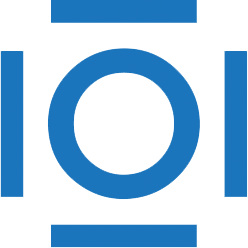
CITATIONS
Cited by 1 scholarly publication.
Finite element methods
Telescopes
Mirrors
Space telescopes
Temperature metrology
Scanning tunneling microscopy
Thermal modeling