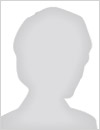
This will count as one of your downloads.
You will have access to both the presentation and article (if available).
PB-DTCO flow can generate plenty of test patterns for model creation and yield gaining, classify candidate patterns systematically and furthermore build up bank includes pairs of match and optimization patterns quickly. Those banks can be used for hotspot fixing, layout optimization and also be referenced for the next technology node. Therefore, the combination of PB-DTCO flow with OPC not only benefits for reducing the time-to-market but also flexible and can be easily adapted to diversity OPC flow.
Using a pattern-based approach to detect all IP Blocks used provides the foundry advanced capabilities to analyze them further for any kind of changes which could void the OPC and process window optimizations. Having any changes in an IP Block could cause functionality changes or even failures. This also opens the foundry to legal and cost issues while at the same time forcing re-spins of the design.
In this publication, we discuss the methodology we have employed to avoid process issues and tape-out errors while at the same time reduce our manual work and improve the turnaround time. We are also able to use our pattern analysis to improve our OPC optimizations when modifications are encountered which have not been seen before.
At advanced nodes, definition of design rules and process options must be tightly optimized to deliver the best tradeoff performance, power, area and manufacturability. However, implementation platforms don’t typically have access to process information and process teams don’t have design knowledge, and optimization loops required for Design-Technology-Co-Optimization (DTCO) are either impossible or at best long and expensive for fabless design house.
Joining forces, ASML, IMEC and Cadence Design Systems developed an In-design and signoff lithography physical analysis well suited for 7/5nm and below. The Tachyon OPC+ engine used by IMEC 7/5nm process has been integrated in Cadence Litho Physical Analyzer (LPA) to perform lithography checks using the foundry process models, recipes, and hotspot detectors. This flow leverages existing LPA infrastructure for both custom and digital design platforms, as well as standalone signoff.
Depending upon the end application, LPA could be launched either from place & route or custom layout or standalone. LPA processes first the design database to identify hierarchy, decompose the layout for coloring and apply pattern matching to identify location requiring simulation. The layout is then passed to the Tachyon OPC tool to perform optical process correction and model-based litho verification that is validated on Silicon. The hotspots and contours are processed by LPA for generation of hotspot marker and fixing guidelines and provide all this information to the design environment.
The flow has been developed and demonstrated to work on IMEC 7nm, and can be ported to smaller or larger technologies. The paper will present the result of this In-design and signoff lithography physical analysis flow, how DTCO and design teams can add manufacturability to PPA.
A new random layout generating method, Design Technology Co-Optimization Pattern Generator (DTCO-PG), is reported in this paper to create cell-based design. DTCO-PG also includes how to characterize the randomness and fuzziness, so that it is able to build up the machine learning scheme which model could be trained by previous results, and then it generates patterns never seen in a lite design. This methodology not only increases pattern diversity but also finds out potential hotspot preliminarily.
This paper also demonstrates an integrated flow from DTCO pattern generation to layout modification. Optical Proximity Correction, OPC and lithographic simulation is then applied to DTCO-PG design database to detect hotspots and then hotspots or weak points can be automatically fixed through the procedure or handled manually. This flow benefits the process evolution to have a faster development cycle time, more complexity pattern design, higher probability to find out potential hotspots in early stage, and a more holistic yield ramping operation.
Accurately predicting copper interconnect topographies in foundry design for manufacturability flows
Automated full-chip hotspot detection and removal flow for interconnect layers of cell-based designs
View contact details
No SPIE Account? Create one